Metal recovery from industrial production waste made possible
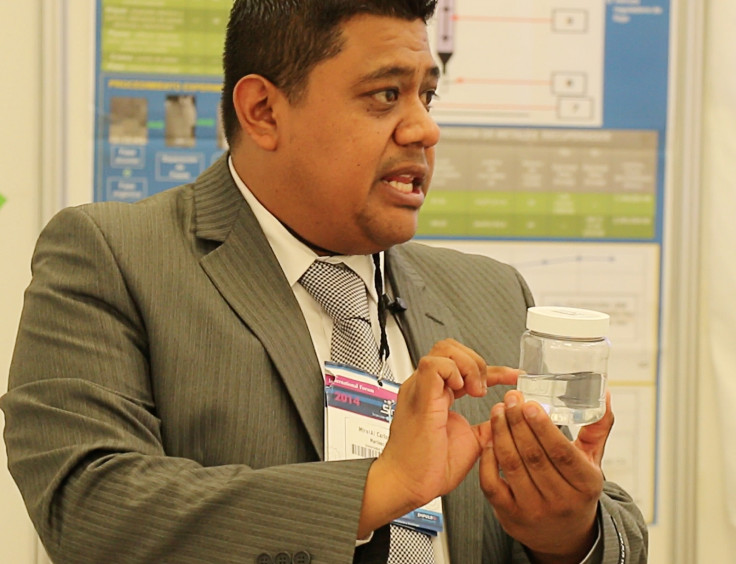
Researchers at the University of Guanajuato (UGTO) in Mexico have developed a method of extraction of metals used by industries in their production processes.
The metal in the solution can be incorporated into the production process or sold to other companies, with no waste thus cutting both economic loss and environmental pollution.
Units producing automotive parts, electronics, tannery and paints are among those that could benefit, says a Agenica ID press release, while adding that any industry using metal in their processes can use the extraction column developed.
The process begins with the extraction when the influent enters the top of the column, makes contact with an organic formulation containing the extracting agent.
These are highly selective for the specific metal sought to be recovered.
When leaving the column, the effluent will be virtually free of metal.
The technology is already at laboratory prototype stage and in the process of obtaining a patent.
Most countries have pollution norms in place to ensure that effluents are treated before they are released into the environment. However, often compliance is lacking as also monitoring.
The lead-acid battery manufacturing industry, electroplating industry and coal power generation facilities are among major producers of metal pollutants.
Heavy metals such as arsenic, cadmium, iron, cobalt, chromium, copper, manganese, mercury, molybdenum, nickel, lead, selenium, vanadium and zinc are some of the common by-products of industrial production and some of these can lead to serious health problems.
Lead levels resulting from industrial effluents have been recorded in Chinese rivers that are some 44 times greater than accepted norms.
© Copyright IBTimes 2025. All rights reserved.