Tiny pop-up robotic arm from Harvard assists doctors with endoscopic surgery
Soft robot arm lies flat inside the endoscope and then pops up at site.
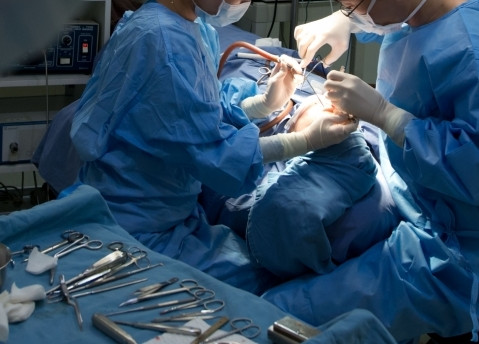
Harvard scientists have built a robotic arm that can make endoscopic surgery easier to perform and is safer for patients by making it soft and flexible. They claim it can be scaled down to a millimetre.
Instruments used by doctors right now in endoscopy are quite flexible, snaking around a patient's body till they reach the site after which the tools themselves are hard and rigid, reducing flexibility, dexterity, and sensing capabilities of the surgeon, according to a Harvard publication.
A team from the Harvard John A Paulson School of Engineering and Applied Sciences and the Wyss Institute for Biologically Inspired Engineering has created a "hybrid rigid-soft robotic arm for endoscopes". The arm has integrated sensing, flexibility, and multiple degrees of freedom, says the publication.
Based on the concepts of pop-up fabrication and soft lithography, the robotic arm will lie flat inside the endoscope till it reaches the target area after which it will pop up and can then be used to conduct intricate surgery.
The arm also has a suction cup, inspired by octopus tentacles that can safely interact with internal tissue.
One of the main features of this device, apart from its pop-up capability is that it has a soft arm. The robotic tools can match the stiffness of the body in such a way that it does not accidentally puncture or tear tissue upon contact which can be a problem with traditional endoscopy, it is reported. However, a soft device at that scale will not damage tissue, but will also not be able to manipulate it in "any meaningful way" said Tommaso Ranzani, a postdoctoral fellow at SEAS and the Wyss Institute and coauthor of the paper.
That being the case, the team had to come up with a way to, "develop soft robots that are still able to generate the necessary forces without compromising safety".
Pop-up robots, inspired by origami are not new, but to make sure that they can be safely used inside a body during surgery, the team had to devise methods that did not need high voltage or generate heat during operation. So they developed fluidic microactuators – water-powered motors, to work the rigid pop-up structures.
The device itself is a combination of rigid and soft materials that work together without the need for adhesives, but make use of "irreversible chemical bonds".
Researchers say that this method can be improved with more sensing and actuation, increasing the complexity of the device based on application and they claim that the pop-up arm can be scaled down to one millimetre so that it can be used in tight spaces like in the brain or lungs.
© Copyright IBTimes 2025. All rights reserved.