Can a new generation of prefab homes solve the UK housing crisis?
The government is reportedly preparing to support the construction of 100,000 prefab homes.
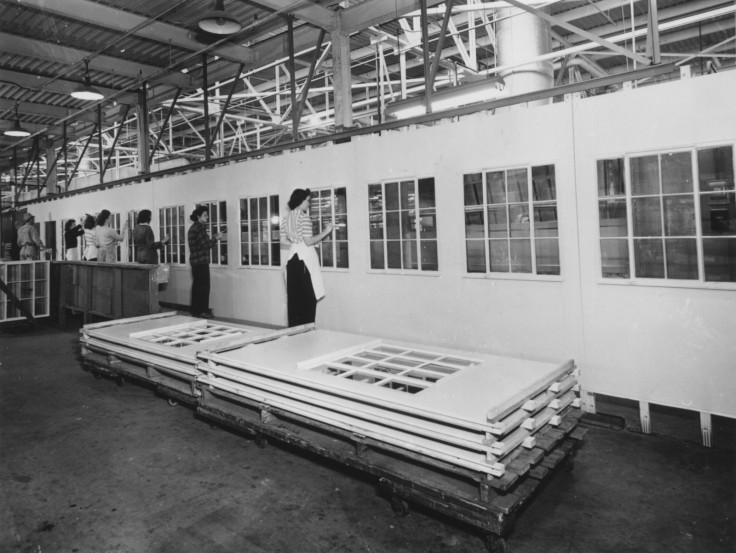
Prefabricated homes, or "prefabs" as they became known, were a quick-fix solution to the country's post-war housing needs. Catastrophic bombing raids on British cities razed residential streets to the ground, leaving many families homeless. So we needed homes, and fast.
Prefabs, manufactured offsite and then assembled onsite, were sturdier than expected. Many still stand today, concrete and steel memorials to their own resilience, despite the initial plan that they would last a decade or so at most. But they are dated, and inevitably, given the era in which they were constructed and the pace they were turned out from the factories, not of high quality.
With modern advances in construction techniques and technology, prefabricated no longer is a byword for low quality. Offsite construction technology has come on leaps and bounds. It's much quicker and cheaper than traditional methods, and the quality has improved drastically. Prefab homes are coming of age in Britain, growing out of their ugly post-war utilitarianism and into an aesthetic-conscious adolescence. Quality homes quickly.
That's why the government is considering using some of its £3bn ($3.66bn, €3.34bn) house building fund to support a new generation of prefabs as a means of easing the housing crisis, says a report in The Sunday Telegraph. It hopes to see 100,000 new homes constructed offsite in this way, a modest target in the scheme of things. Details should be revealed in the government's white paper on housing, due to be published in November.
The government has committed to building a million new homes by 2020, but housing completions are currently well short of achieving this goal. There were just 142,390 completions in England and Wales in 2015. Prefabs can go up in as short a time 48 hours, drastically quickening the construction process, bringing the million homes target closer into reach.
"Offsite construction could provide a huge opportunity to increase housing supply and we want to see more innovation like this emulated across the housebuilding sector," Gavin Barwell, the housing minister, told the newspaper.
Skills and materials shortages blight the construction sector, increasing the cost of house building and holding back output. Brexit threatens to worsen the skills shortage even more by restricting the flow of European labour, which accounts for around 10% of the construction workforce across the whole of the UK, and around a third in London specifically.
Yet the government wants to significantly increase housing output to near 250,000 new units a year. "We simply don't have the capacity to do that," said Abdul Choudhury, London policy manager at the Royal Institution of Chartered Surveyors (Rics).
But offsite construction is more efficient with both labour and materials, Choudhury said, and the country is a long way from utilising the full potential of prefabrication in housing, especially compared to other European and Western states. So there is space for it to grow as a sector, one that isn't a panacea for the housing crisis, but can deliver more homes faster if we utilise it.
As for the public, the perception persists of prefab as a bleak, unforgiving means to an end in the post-war years, one that hinders a shift towards offsite construction. But things are different now, and modern prefabs must be seen to be believed. "I think when people start to see what prefab actually means nowadays, they'll adapt very quickly," Choudhury said, citing the attractive home designs by German prefab manufacturer Huf Haus.
Others are sceptical, however. The housing shortage, which has driven up house prices and rents, particularly in London and the south east of England, two of the most affected areas, has fundamental causes not solved by ratcheting up the number of prefabs, they say.
"British housing costs, as it has done for generations, around and about what it costs to build a house," wrote Tim Worstall, senior fellow at the Adam Smith Institute, a pro-free market think tank, on the organisation's blog.
"Lowering that cost through more efficient housebuilding is to be welcomed, of course. But that's not the problem we face. The problem we do face is that the cost of a piece of land, with the associated chitty to allow a house to be put on that land, is extortionate.
"And the reason for that is that we've an immensely restrictive planning system that horribly limits which piece of land you can put a house on."
Whether or not it is the solution to the housing crisis, prefab looks to be the next growth area for the house building industry in the UK. Some are already putting their money where their mouth is. In February 2016, L&G unveiled £55m plans to build the world's largest modular housing factory in the world, just outside of Leeds. It's likely others will follow, especially if the government is throwing its weight — and money — behind the sector.
© Copyright IBTimes 2025. All rights reserved.