Ultra-strong fibre based on spider silk made in lab
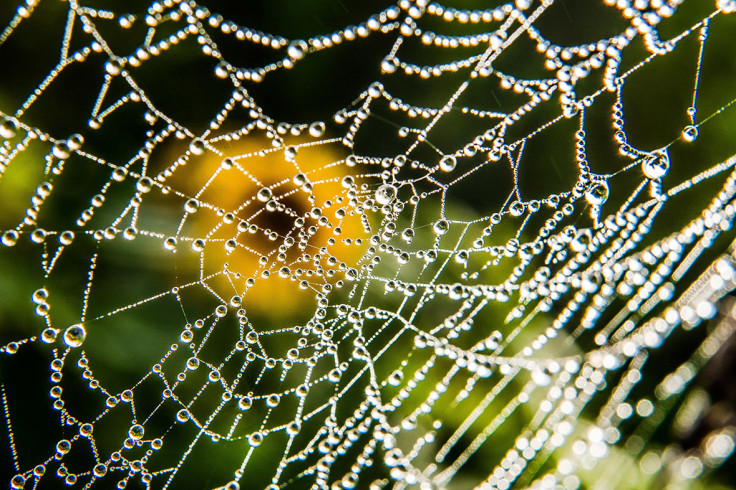
Researchers at Polytechnique Montréal have produced an ultra-tough polymer fibre based on the structural composition of spider silk.
Tougher than steel and less than a quarter of a hair's width, spider silk owes its exceptional strength to the molecular structure of its protein chain.
Coiled up like a spring, the protein loops are attached by strong chemical bonds to its neighbours.
"To break the protein by stretching it, you need to uncoil the spring and break each of the sacrificial bonds one by one, which takes a lot of energy. This is the mechanism we're seeking to reproduce in laboratory," explained Frédérick Gosselin, who, along with Daniel Therriault, is co-supervising Renaud Passieux's research work.
The project involved making micro-structured fibres similar to spider silk in a process that draws on concepts from fluid mechanics, microfabrication, materials research, polymer rheology and more.
The team from the Laboratory for Multiscale Mechanics at the Polytechnique's Department of Mechanical Engineering was able to develop fibres that required a strong energetic pull to be broken apart.
"It consists in pouring a filament of viscous polymeric solution toward a sub-layer that moves at a certain speed. So we create an instability," said Passieux.
"The filament forms a series of loops or coils, kind of like when you pour a thread of honey onto a piece of toast. Depending on the instability determined by the way the fluid runs, the fibre presents a particular geometry. It forms regular periodic patterns, which we call instability patterns."
The fibre solidifies as the solvent evaporates. The rope coiling instability leads to formation of sacrificial bonds as the filament makes a loop and bonds to itself.
The article is published in the journal Advanced Materials.
Composites obtained by weaving together such tough fibres could be used to build safer and lighter casings for aircraft engines that hold the structure intact even during an explosion, surgical devices, bullet-proof clothing and vehicle parts.
© Copyright IBTimes 2025. All rights reserved.