Nasa Creates First 3D-Printed Object in Space on the International Space Station
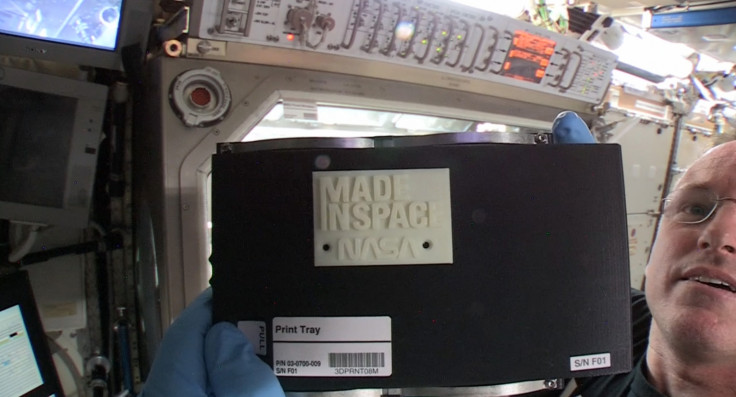
Nasa astronaut Barry "Butch" Wilmore, the commander of Expedition 42 aboard the International Space Station (ISS), has created the first ever 3D-printed object in space.
Wilmore installed the ZeroG 3D Printer on the ISS on 17 November and performed the first calibration test print.
Zero-G is the first 3D printer ever designed to operate in zero gravity, and is the result of a research collaboration between Nasa's Marshall Space Flight Center and 3D-printing technology company Made in Space.
The results of the first test print were send to ground control, who then sent back new calibration commands to realign the printer over the next few days. A camera is set up next to the printer so that ground control can monitor each layer being printed.
Finally on Tuesday, the printer was ready and ground control sent the command for Zero-G to print out the first object made in space – a faceplate that will serve as an access panel to the print head's extruder.
The faceplate is made from Acrylonitrile Butadiene Styrene (ABS) plastic, a common plastic polymer used by many 3D printers today.
The Zero-G 3D printer is able to print at a speed of 40mm per second, and the 3D-printed object demonstrates that the 3D printer can make replacement parts for itself.
But even more importantly, being able to 3D print items in space would be hugely helpful in enabling astronauts to be able to fix critical problems and replace crucial tools during a mission.
"We chose this part to print first because, after all, if we are going to have 3D printers make spare and replacement parts for critical items in space, we have to be able to make spare parts for the printers," said Niki Werkheiser, project manager for the International Space Station 3D Printer at NASA's Marshall Space Flight Center in Huntsville, Alabama.
"If a printer is critical for explorers, it must be capable of replicating its own parts, so that it can keep working during longer journeys to places like Mars or an asteroid. Ultimately, one day, a printer may even be able to print another printer."
Nevertheless, it will still take some time before Zero-G will be able to print out replacement parts and tools, as ground control needs to make sure that the parts are of an acceptable standard.
"This is the first time we've ever used a 3D printer in space, and we are learning, even from these initial operations," said Werkheiser.
"As we print more parts we'll be able to learn whether some of the effects we are seeing are caused by microgravity or just part of the normal fine-tuning process for printing.
"When we get the parts back on Earth, we'll be able to do a more detailed analysis to find out how they compare to parts printed on Earth."
Nasa is not only working on 3D-printing within spacecraft, but also on 3D-printed parts that are strong enough to be used on the exteriors of spacecraft and survive the harsh conditions of outer space.
Red Eye, a subsidiary of Stratasys, has been working with Nasa's Jet Propulsion Laboratories on manufacturing parts to mend Nasa's Cosmic-2 satellites, using a 3D-printing technique called Fused Deposition Modeling (FDM) to print out parts from ULTEM 9085 material.
ULTEM 9085 is a durable thermoplastic with similar properties to metal and has been proven to be a good replacement for the traditional astroquartz material.
© Copyright IBTimes 2025. All rights reserved.